Logistex provide automated materials handling and software (WMS) solutions for warehousing operations. We are specialists in storage and retrieval, order forwarding, picking and sortation systems. As an independent warehouse automation specialist, we integrate products from across the industry without compromise. Our services cover warehouse/materials handling design & implementation, warehouse management software and control systems, equipment refurbishment and maintenance, facilities management and 24/7 hotline support and spares.
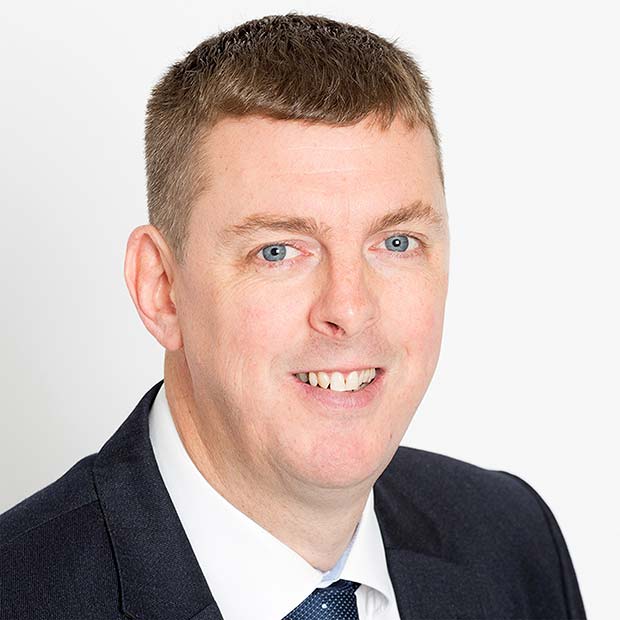
Business Development Director at Logistex
Justin Saw, Business Development Director at Logistex spoke to Warehouse & Logistics News.
What products or services does your company offer?
Our offering to the market encompasses a wide range of technologies to which we have been particularly successful recently in delivering fully Automated Pallet Shuttle and Tote Shuttle solutions. We are also increasingly becoming engaged in robotic based projects as this technology becomes increasingly viable.
Our key services include Solution Design, which is supported by full simulation and virtual reality to enhance customer experience and provide proof of concept, emulation, WMS, Project Implementation and Engineering support services.
Which industries do your customers operate in?
E-com remains a very large growth area for Logistex. Ongoing challenges within the labour market, and the need to fulfil orders in the quickest possible time, at the lowest cost, leads Clients to explore the benefits of automation. Both new and existing customers are regularly challenging us to provide innovative solutions in this area.
Similarly, Food and Drink and Apparel remain growth sectors.
Logistex have also successfully delivered a multi-award-winning project within the Pharmacy industry, which was the first of its type. Both the solution design and software requirement ensured we utilised the core strengths of the business.
Has your company celebrated any milestones this year?
Following 15 years as Managing Director at Logistex, Jerry Woodhouse has moved to the role of Chairman. Jerry will continue to lead a range of Company initiatives including championing health and safety. Tony Gruber has been promoted to Managing Director. His role at Logistex is to provide overall leadership in developing future business strategy and to ensure existing operations constantly meet or exceed the demands of our customers.
Do you have any examples of a project you have recently completed?
Logistex has just installed a 54,000 tote shuttle project for a major UK retailer, which has been a great success. Equally over the last 12 months we have completed a series of smaller conveyor based projects for ecom customers.
Do you think some of the trends that began or were accelerated during Covid-19, such as the increase in e-commerce, will become permanent?
There are tens of thousands of new on-line customers who are likely to continue enjoying the convenience of ordering online, long after lockdowns have become a distant memory.
The pandemic aside, there was always a broader labour force question when it came to manual picking in warehouses. Increasing labour shortages and increasing costs suggest that warehouse operators will need to identify a way to work more efficiently. Automation is very much considered to be a viable option.
If logistics operations are to learn how to adapt to, and maximise, a new post COVID-19 economy, then order fulfilment strategies based on automation and robotics will be vital.
What improvements have you made to your customer service recently?
Logistex has increased the number of mobile engineers ensuring we are able to offer an agile response to our customer’s needs. As well as offering 24/7 cover we now offer a service portal to allow supported customers to raise incidents and service requests, review open tickets and run reports based on ticket history with the ability to export the results. This doesn’t replace telephone or email with our Service Desk, but gives customers an additional channel for improved flexibility to suit their own needs.
Are you helping customers boost the level of automation in their business?
That’s what we’re all about. Whether a customer has a manual operation and is looking to take their first steps into automation, or they have existing automation that needs modifying, or perhaps a completely new build where the concept needs to be designed from scratch; Logistex provide innovative solutions to any automation application at any stage of the journey.
Do you help customers maximise the use of their existing warehouse space?
Yes, our automated pallet shuttle and tote shuttle solutions lend themselves particularly well to optimising use of space.
Will you be exhibiting at any major trade shows in 2022?
We will be attending the Retail Logistics & Supply Chain Expo at the ExCel on 2nd-3rd March, as well as IMHX at the NEC on 6th-8th September. It is so important to keep updated with product enhancements and new technologies, and exhibitions provide an excellent platform for Logistex to engage with new and existing customers. We are looking forward to sharing our knowledge about all things automation, but with a particular focus on pallet shuttle, tote shuttle and AMR technologies at these exhibitions.
How future proof is your business?
Logistex are not an equipment manufacturer so are able to maintain a position to integrate leading technology within our solutions. As a company we have agreed partnerships with a number of leading equipment providers. This allows us to work with particular suppliers to develop products to meet with our customers future needs.
Annually we also run Group meetings with our existing customers to identify future needs and requirements. We run a series of workshops around pre-selected themes to consider the future needs and the role we will need to play within this.
What sets your company apart as a supplier in your category?
Being independent we have a key advantage in that we can provide an unrivaled solution in integrating the best equipment from a wide range of suppliers. We are an employee-owned business, which allows our employees to share in the success of the business, and enables us to offer a higher level of engagement with our team. This has been particularly evident in some of our more recent projects where we have been able to provide better overall throughput and performance using proven equipment, which further reduces risk.
As a business we also offer a 24/7 hotline and support service which is provided by Logistex employees, which is highly valued by our clients.
How would you sum up your company in three words?
Experts in automation
LOGISTEX
01536 480 600
Comments are closed.