Geek+ is a global technology company leading the intelligent logistics revolution. We apply advanced robotics and AI technologies to realize flexible, reliable, and highly efficient solutions for warehouses and supply chain management. Geek+ counts 300 global customers and has sold more than 20,000 robots worldwide. Founded in 2015, Geek+ has over 1,500 employees and is headquartered in Beijing, with offices in Germany, the UK, the US, Japan, Hong Kong, and Singapore.
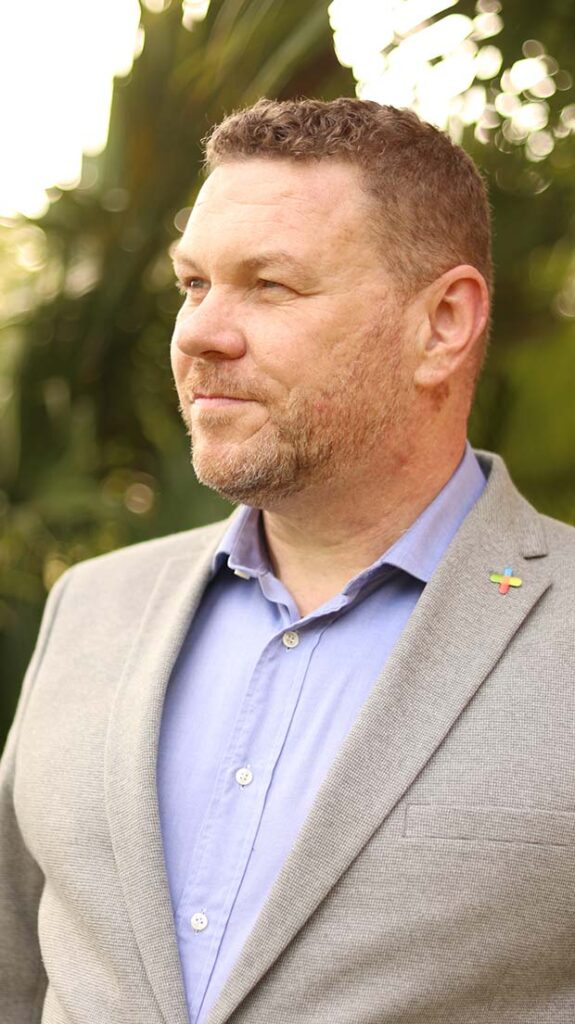
Head of Sales and Marketing at Geek+
Simon Houghton, Head of Sales and Marketing at Geek+ spoke to Warehouse & Logistics News.
What products or services does your company offer?
We provide companies with Al-driven robotics solutions that automate some of the time-consuming tasks that are often done manually in a warehouse or a factory, like walking long distances to find ordered goods and carrying items back and forth. Powered by AI and intelligent scheduling or task distribution, our robots can move autonomously around the warehouse and optimally execute various tasks, bringing more efficiency and accuracy to warehouse and factory operations. In terms of hardware, we have a full range of robots that can be divided into picking, moving, sorting, and smart forklifts. Many of these can be integrated and work together to automate certain processes. We also have full-automation solutions like Smart Warehouse and Smart Factory; these can combine our different robots to automate entire operations. All of these can be tailored to meet the specific needs of the customer and integrate into existing infrastructure.
Which industries do your customers operate in?
Our solutions are highly flexible, allowing them to be used in a wide range of industries. We have already helped clients in the apparel, e-commerce, retail, 3PL, pharmaceuticals, automotive, 3C manufacturing, FMCG, and express delivery sectors to undertake digital transformation.
Has your company celebrated any milestones this year?
Last year, we introduced RoboShuttle ® tote-to-person solution to the market. This series of double-deep robots are designed to work in narrow aisles to help businesses to achieve high-density warehouse storage and high picking, storage, and operating efficiency. And we have also helped Asda Logistics Services achieve 99.99% operational accuracy and streamline Asda’s toyou service. This solution was awarded the Supply Chain Excellence Innovation Award 2021 in recognition of our accomplishment.
Do you have any examples of a project you have recently completed?
In the UK, we deployed sixty sorting robots in Asda’s distribution centre together with AMH Material Handling. This is a very successful development in the warehouse robotics market in UK. At the global level, we have assisted several well-known companies in many industries to get on the journey of warehouse 4.0, such as grocery giant Circle K, well-know ecommerce site Catch.com and 3PL leaders UPS, Geodis, Rhenus, etc.
How did your company react to the Covid-19 outbreak and consequent lockdowns?
We have already set up local supporting teams in numerous regions before COVID-19, so the lockdowns didn’t have a huge impact on us. To further improve our service level, we established local offices in the UK, Germany, Singapore, etc. Because our customers are present in over 20 countries, these offices can give our clients the most timely and localized support and assistance.
Over a year on from the start of Covid-19, what lessons has the company and the industry learned from the pandemic?
Businesses are facing a slew of unanticipated changes in the Covid-19 pandemic. To assist them in dealing with this out-of-the-blue situation, we understand that our solutions need to be highly flexible to enable them to respond quickly. We also collaborate with our clients to provide a customized solution precisely tailored to their needs. With our strong R&D capabilities, we will continue to develop more high-performing products and solutions to help the industry.
Do you think some of the trends that began or were accelerated during Covid-19, such as the increase in e-commerce, will become permanent?
We have seen many of our clients choose our solutions for automatic warehouse solutions to support their growing e-commerce business and we believe this trend will continue. Convenience is a huge reason for customers to change their shopping behaviour from shopping at brick-and-mortar stores to purchasing online. To provide a better shopping experience to their customers, businesses are striving hard to provide speedy delivery such as same-day or next-day delivery. To achieve this objective, they adopt our solutions to optimise warehouse operations, increase operation efficiency and set up micro-fulfilment centres. Because order processing takes less time, parcels can arrive at the customer’s address earlier.
What products or services will you be introducing in the next year?
Next year, we will roll out the PopPick workstation. Our P series robots carry the movable shelves to the PopPick workstation, where the target totes are automatically taken out and sent to the operator. With an ergonomic PopPick workstation, picking efficiency could reach 650 totes per hour. Meanwhile, this solution is compatible with large goods and whole pallet picking, meaning one solution solves the storage and picking needs of small, medium, and large items, which all bring great convenience to warehouse operations.
Combined with our 4-way shuttle system, the warehouse could achieve high-density storage with picking. With this integrated solution, warehouse owners could increase warehouse storage capacity by fully utilising the vertical space. And, combined with our full-range robots, this is a one-stop automation solution for warehouses.
What improvements have you made to your customer service recently?
Geek+ provides a 24/7 customer service hotline for our global clients, as well as a team of professional technicians to be on standby for customer inquiries. We have also implemented a “localization” strategy by setting up regional offices with sales teams, channels, and service partners to provide products and services in local languages, adapted to customers needs and requirements. Our after-sales support is highly developed and includes a 24/7 helpdesk, remote maintenance, on-site repair, system maintenance, and upgrade support.
Are you helping customers boost the level of automation in their business?
Yes. Our solutions are centred around the idea that automation can provide many benefits to several industries. Traditional fixed automation equipment has several downsides, such as a large amount of upfront investment, long lead times, complex operation, difficult maintenance, and a lack of flexibility. Comparatively, our robots can autonomously navigate the environment, which brings flexibility and scalability to the solution. The stage-based deployment and rapid implementation don’t require a large modification of on-site hardware or the existing warehouse layout, so it can be finished in a short time, making it easy for our clients to scale operations in line with business growth and peak seasonal demand.
Will you be exhibiting at any major trade shows in 2022?
We will keep participating in key industrial events in the UK, such as IMHX 2022, the Robotics and Automation Show and Intralogistex. Global events, such as ProMat (US) and CeMat global will also be our focus. We are currently looking at opportunities to exhibit in Ireland, as well.
Geek+
+44 0800 048 7268
Comments are closed.