Waste is a huge issue across the supply chain industry and many of the UK’s largest supermarkets, including Tesco, Sainsbury’s and Waitrose, as well as food and drinks manufacturers, have committed to halve food waste by 2030. According to the Department for Environment, Food and Rural Affairs, the UK currently generates 10.2 million tonnes of food waste each year.
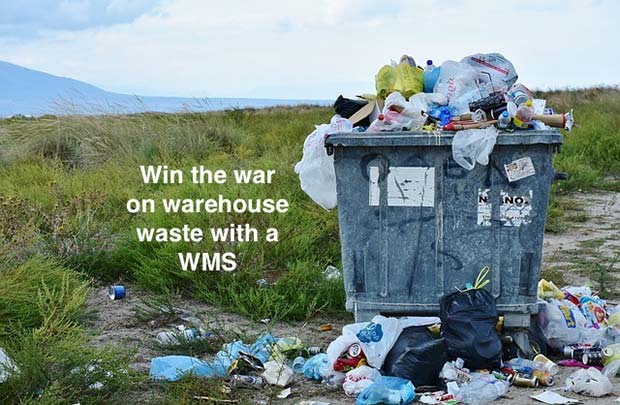
Of that total, 1.8 million tonnes comes from food manufacturing, one million tonnes from the hospitality sector, 260,000 tonnes from retail and the rest from households. Businesses are being urged to cut back on waste as part of the government’s Food Waste Reduction Roadmap.
A key aspect of waste control needs to be driven by the warehouse and here there are 3 main things for food warehouses to minimise.
• Waste in terms of energy consumption and how to minimise the unnecessary use of energy in the warehouse, including transportation costs;
• Waste in terms of resource consumption including labour costs in the warehouse. Manpower is a huge cost in most foods warehouses, especially if they need to manage demand seasonality or perishability. By optimising pick path planning and product slotting, pick speeds can be increased by up to 20%.
• Waste in terms of the utilisation of packaging and materials consumption in the warehouse. This article will deal with a range of these issues, looking in turn at how a Warehouse Management System (WMS) can help to accelerate your organisation’s adoption of the government’s Waste Reduction Roadmap, by minimising waste in your warehouse.
Efficient Inventory Management
Manufacturing waste can be reduced by carefully controlling the materials being used in the manufacturing process and a WMS can support this in different ways.
Firstly, by helping to ensure that raw materials inventory is being rotated efficiently and utilised well within shelf life. When stock comes into the warehouse, it is receipted by the WMS, according to a set process, which includes recording the delivery date, use by date and successful completion of a range of quality checks to verify its condition upon arrival. Stock is then marked as available for production and when allocating materials required for a production run, the WMS will automatically select raw materials inventory according to ‘first in first out’ principles, or specific rules set by warehouse management.
Secondly, by operating in realtime, the WMS helps a production facility adhere to lean manufacturing principles through real-time inventory visibility and the ability to match available inventory to demand forecasts. Better demand management will make your warehouse more responsive to customer requests and reduce out of stocks – as well as reduce costs through limiting the risks of stock damage, obsolescence and overstocking situations where goods are stored unnecessarily.
One of the biggest costs in any manufacturing operation is stock. By minimising the amount of stock being held and ideally, pushing it as far down the supply chain as possible, an organisation can be as efficient as possible. Currently, many manufacturers are being forced to stockpile and hold excess inventory, due to fears of shortages as a result of a no-deal Brexit. Aside from the costs of purchasing and holding this extra stock, there is the risk of spoilage due to poor rotation management and using a WMS helps keep this risk to a minimum.
Reduce packaging materials wastage At Budget 2018, the government announced that from April 2022, it would introduce a new tax on the production and import of plastic packaging with less than 30% recycled content. This is a way off, but consumer attitudes towards the unnecessary use of plastics and wastage is already accelerating the transition. As a result, many manufacturers are currently phasing out older packaging designs in favour of newer, more environmentally friendly solutions.
This is a long term process and can be controlled automatically using a WMS. To minimise wastage, it is important to be able to utilise this old stock for as long as possible, rather than dispose of unused packaging into landfill. In the same way as a WMS supports raw materials inventory, the same principal applies to packaging materials, with stocks rotated to meet corresponding use by dates and incoming legislation.
Optimised warehouse layouts
One of the biggest sources of wastage in a warehouse is time – the time operatives take walking or driving between locations, looking for stock on the picking lists or searching for putaway locations. According to CBRE estimates, manual picking methods mean 75- 80 per cent of employee time is spent walking the warehouse floor. A WMS automates this entire process, by learning where items should be stored for maximum efficiency and reducing conveyance, the unnecessary carrying and movement of inventory from one location to another. In addition to reducing labour costs, optimising layouts reduces energy costs by introducing a demand based flow, making fast-moving stock more accessible and reducing travel times throughout the facility.
KPIs to improve through better waste management
As a result of improving waste management with a WMS solution, here are just some of the KPIs you can expect to improve:
Order Fulfilment
On-Time Delivery % = Orders On- Time vs Total Orders Shipped Perfect Order Completion % = Perfect Deliveries vs Total Orders Shipped
Inventory Management
Damaged Inventory % = Total Damage £ vs Inventory Value £ (Cost) # of Days on Hand = Average Month Inventory £ vs Average Daily Sales / Month Storage Utilization % = Average Occupied Square Meter vs Total Storage Capacity
Warehouse Performance Metrics
Orders per Hour = Orders Picked / Packed vs Total Warehouse Labour Hours
Cost per Order = Total Warehouse Cost vs Total Orders Shipped
Putaway
Putaway Cost x Line = Cost of Putting Away Stock per Line (labour, handling + equipment)
Putaway Cycle Time = Total Time Taken during the entire process of each Putaway task
Storage
Carrying Cost of Inventory = Storage Cost Over a Determined Period of Time. It includes: cost of inventory + capital + damage + service + cost of obsolescence Space Utilisation = (Warehouse Space Used / Total Warehouse Space) * 100%
Picking & Packing
Picking Accuracy = % of Orders Picked and Packed without any Incident Picking Cycle Time = Time Taken to Pick each Order
INDIGO SOFTWARE
Comments are closed.