BAYTREE LOGISTICS PROPERTIES
The first phase of Baytree’s two-part warehouse unit development in Dunstable has environmental, community and social features at the heart of its design.
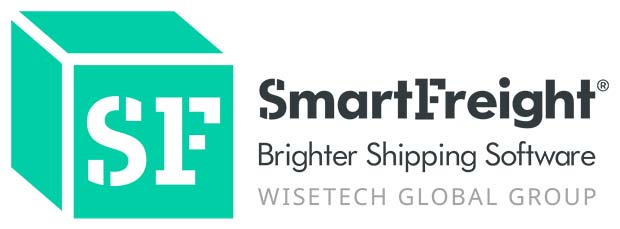
In terms of green innovation, technology and design, the development was planned and constructed through a full Building Information Modelling (BIM) model, coordinating through a 4D timeline video. This provided high quality visualisations and a digital interactive platform of all the build information, which could be accessed remotely.
Drones were used to produce volumetric measurement for earthworks, exporting drone generated data directly into the BIM model and providing access to relevant and accurate information.
A key feature of the development is a comprehensive sensor suite installed in the offices which monitors external air quality, indoor air quality, humidity levels, noise levels, temperature and occupancy levels and reports back to a dashboard within the reception area and the building BMS. It can be set-up to control heating/cooling requirements and lighting levels dependent on occupancy.
DURABLE UK
Durable is a German manufacturer of workplace solutions. In the UK – the largest of the company’s 12 global subsidiaries – Durable operates a 1,200 square metre warehouse which holds over 1,000 products for next day delivery.
Durable installed low-energy lighting at the UK site a number of years ago and, in 2017, replaced 103 office lights with low energy LEDs which are expected to save 51 tonnes of CO2 over the course of their lifetime. In addition, all lights throughout the warehouse and offices are motion sensitive, which means they save energy when not needed.
Durable UK’s investment in low-energy office lighting has reduced energy consumption and therefore reduced energy costs. Electricity used to power the office lights has dropped from 22,831 to 6,610 KWh/year and so the annual spend on electricity has reduced by over 70%. In addition, early in 2016, Durable UK installed solar panels. The solar panels produce enough electricity to power all electrical needs within the building. In all, 90,645 kWh of electricity has been generated by the panels since February 2016, this equates to 64.1 metric tonnes of CO2 emissions saved.
E-CARGOBIKES.COM
e-cargobikes.com is a zero-emission last-mile ‘all-in’ delivery service for national retailers and grocers designed to offer an alternative to the diesel van delivery platform. A trial of the company’s electrically assisted bicycles with Sainsbury’s in spring 2018 exceeded all client KPIs by reducing delivery times, delivery costs, air pollution, Co2 emissions and congestion and, as a result, e-cargobikes.com is now working with other major UK retailers to establish a network of e-cargobike hubs in urban centres across the UK. For example, earlier this year, e-cargobikes.com launched Co-op’s home-delivery service in Chelsea and is currently rolling this service out across London.
One e-cargobike and one rider can deliver the same weight and volume of produce as a 3.5t van over an 8 hour shift. With a carrying capacity of 125 kg, one ecargobike can deliver 96% of grocery orders and the remaining 4% of orders, typically bulkier items, can be carried by two e-cargobikes delivering in tandem. James FitzGerald, co-founder of ecargobikes. com, says: “Large scale modal shift from van to e-cargobike delivery will result in hitherto unimaginable environmental improvements.”
EUROPEAN TYRE ENTERPRISES LTD WITH ECOLIGHTING
European Tyre Enterprise Ltd (ETEL) is the UK’s largest tyre distribution and retailing company, and includes the Stapletons and Kwikfit brands. Ecolighting has just completed an upgrade of the lighting within ETEL’s portfolio of storage and distribution facilities and new LED lighting has been installed in the warehouse aisles, at mezzanine level, in the despatch areas, under the external canopies, in the car parks and in any office space.
The entire refit programme was completed in all of ETEL’s UK warehouse locations within just a few months, and the impact has been immediate. The reduction in energy usage across the network has reached 50 per cent and some 1,174 tonnes of CO2 has been saved from the company’s carbon footprint. The scale of the financial savings generated mean that the project is delivering a very short return on investment, with payback averaging just one year and nine months across all the distribution centres.
In addition, the feedback from the company’s warehouse staff has been very positive, confirming that the new lighting has made for a more pleasant and efficient working environment.
Comments are closed.