When it comes to the discussion of picking software in the warehouse, perhaps it’s important to refer to it as pick and pack software, because the focus on the packing function within the overall workflow and execution of order fulfilment should not be minimised, writes Chandru Palaniyandi, Business Analyst, Lucas Systems. Like other steps in the fulfilment process, the primary goal of the packing function is to ensure accurate and safe delivery of goods to the end-users while optimising efficiency and minimising errors.
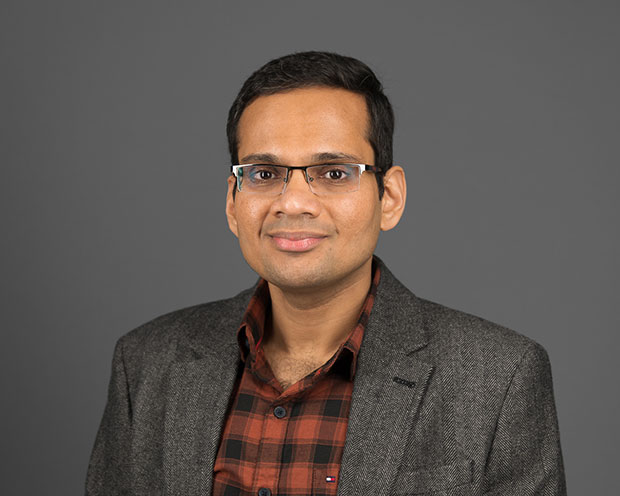
Key elements of packing include:
•Order verification – Before packing begins, warehouse staff must verify the accuracy of the items in each order against the provided order information. This step helps prevent shipping errors, thus reducing costs, and ensures that customers receive the correct products.
•Efficient packing techniques – Optimising the arrangement of items within the packaging to maximise space and minimise voids is crucial. Efficient packing helps reduce shipping costs, as it minimises the number of packages required and ensures that goods are less likely to be damaged during transportation.
•Labeling and documentation – Accurate labeling is critical for tracking and identifying packages throughout the shipping process. Each package should be labelled with the correct shipping address, tracking information, and any other relevant details, including documentation for both the customer and the shipping carrier in many cases.
•Quality control – Before finalising the shipment, quality control checks may be performed to ensure that all items are in good condition, the packaging is secure, and the order is complete. This step helps minimise the likelihood of returns and customer dissatisfaction.
•Integration with shipping systems – The packing function is often integrated with shipping systems to generate shipping labels, track packages, and communicate with carriers. Automation in this process helps streamline operations and reduce manual errors.
The importance of the packing function within a warehouse lies in its impact on customer satisfaction, operational efficiency, and cost-effectiveness. Accurate and secure packing helps in building trust with customers by delivering orders on time and in good condition. It also contributes to the overall workflow by connecting receiving, picking, and shipping processes seamlessly.
Efficient packing practices contribute to:
•Reduced shipping costs – By optimising packaging and minimising wasted space.
•Faster order fulfilment – Streamlining the packing process speeds up overall order processing.
•Fewer returns and errors – Proper packing reduces the likelihood of shipping the wrong items or damaging products during transit.
Packing solution speeds fulfilment and order completion
Headquartered in Coleshill near Birmingham, U.K., Silmid, a part of the Graco Roberts family of companies, is a specialist distributor of chemical consumables used throughout aerospace and aviation, for both OEM and MRO, supplying customers in over 100 countries for 40 years.
With a key value proposition of providing the on-demand supply of small volume orders primarily via its full service B2B ecommerce. They store more than 5,000 SKUs at the Coleshill facility and process in excess of 240 different orders per day, equating to about 60,000 individual orders per year.
Prior to working with Lucas Systems, because of their unique customer requirement, they had experienced issues with orders being left too long at packing and missed shipments. Impressed with Lucas’ capabilities in supporting staging and packing improvements, they asked them to help optimise this function as part of their software implementation.
The Lucas solution for Silmid included tracking the packing time and showing packing productivity stats.
Lucas built process and visibility around staging and packing that offered:
•Staging confirmation – Pickers confirm what location they stage each order.
•Staging visibility – A screen displaying the time each order has been staged, along with the order details.
•Packing confirmation – Packers select and confirm what order they have collected to pack.
•Packing productivity – Packing productivity by user (# of orders/lines/pieces) recorded and reported on management console.
Besides tracking the packing time and showing packing productivity stats, orders staged for packing are listed in priority sequence. The system also shows how long the orders have been at staging (i.e., waiting to be packed). This gives the packers a sense of which orders they need to pack next.
The optimisation gains achieved through the Lucas implementation included 99.9% order accuracy, 35% efficiency gain and a 60% improvement in throughput.
The packing function is a critical component of warehouse operations, directly impacting the customer experience and the overall efficiency of the supply chain. Warehouse managers need to continually seek to improve packing processes through technology, automation, and best practices to stay competitive in the dynamic world of logistics and e-commerce.
About the Author
As a business analyst for Lucas Systems, Chandru Palaniyandi optimises warehouse operations and transforms user experience by leveraging his commitment and knowledge in designing innovative solutions that help companies achieve their supply chain goals.
With more than 10 years of experience in the supply chain domain, Chandru started his career as a software engineer building a warehouse management solution for one of the world’s largest sports footwear and apparel brands. That experience has driven a unique ability and insight around warehouse optimisation through effective business processes, labour management, robotics and artificial intelligence.
About Lucas Systems
Lucas Systems helps companies transform their distribution center by dramatically increasing worker productivity, operational agility, and customer and worker satisfaction using intelligent software with speech recognition and AI optimisation technologies.
Comments are closed.