Managing a warehouse involves much more than receiving, storing, and dispatching goods. It also requires significant planning to ensure operations are conducted safely and in an orderly manner. To achieve this goal, managers need to adopt a holistic approach that includes the correct choice of protective equipment, implementation of emergency protocols, and ongoing training. Learn more.
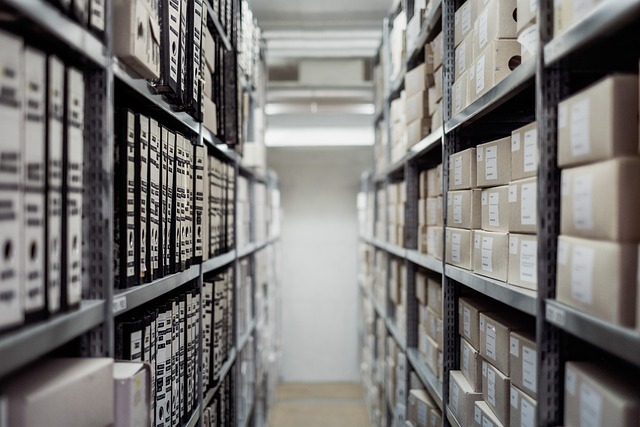
Are Warehouses Dangerous?
Warehouses are vital to the economy and create thousands of jobs in the United Kingdom. However, there is no doubt that these facilities can indeed be dangerous. For example, forklifts and pallet jacks can collide with other vehicles, objects, or even people, causing severe injuries, particularly in areas with narrow aisles. Additionally, objects can fall from these machines and strike nearby individuals.
Lack of proper training can result in loads being dropped during sharp turns or sudden stops. Accidents caused by lack of maintenance, such as brake failure or hydraulic problems, must also be considered. Finally, many forklifts emit pollutants that can accumulate and lead to the development of respiratory illnesses over the long term.
Slips, trips, and falls are common, especially if there are spills, uneven floors, or poorly maintained walkways. Lifting, moving, and packing goods can lead to musculoskeletal injuries, particularly if proper techniques are not used or workers are not adequately trained. Repetitive tasks and inadequate workstation design can contribute to long-term health issues. Moreover, storing hazardous or flammable materials in some warehouses adds another layer of risk.
Warehouse Safety: A Statistical Overview
The risk associated with working in warehouses is highlighted by the latest statistics released by the Health and Safety Executive (HSE). According to the agency, there were 135 work-related fatal injuries in Great Britain in the year 2022/23, with 15 of these fatalities occurring in the transport and storage sector, which includes warehouse activities. Additionally, 3,350 workers reported work-related illnesses, and 1,860 employees sustained non-fatal injuries.
The most common causes of non-fatal accidents in the UK, considering all economic sectors, are slips, trips, or falls on the same level (32%); handling, lifting, or carrying (17%); and being struck by moving objects (11%).
Top Safety Equipment and Procedures
While numerous risks are inherent in the industry, a range of specialised equipment and protocols are available to effectively minimise these threats.
- Personal Protective Equipment (PPE)
Explain to your team the importance of using hard hats to protect the head; safety goggles, particularly near areas with debris or hazardous materials, and high-visibility clothing on sites with vehicle traffic and heavy equipment. The use of steel-toe boots should also be encouraged.
- Material Handling Equipment
To mitigate the risk of muscular issues, investing in equipment that eases the team’s workload and boosts productivity is key. This includes forklifts, pallet jacks (available in manual and powered versions), and conveyor belts. It’s essential to ensure that the team is adequately trained and, where necessary, certified to operate this machinery.
- Safety Signage and Markings
Use floor markings to delineate walkways, forklift paths, and hazardous areas; and warning signs to indicate dangers like forklift traffic, high noise levels, or chemical hazards.
- Fire Safety Equipment
The facility must be equipped with fire extinguishers, sprinkler systems, fire alarms and smoke detectors, all of which must be regularly inspected, clearly marked, and easily accessible.
- Emergency Procedures and Training
Creating and disseminating emergency procedures so everyone knows what to do in case of accidents is crucial. Make sure the warehouse has evacuation plans and escape routes, as well as clearly marked emergency exits and meeting points. Maintain first aid kits in strategic areas and conduct regular emergency training.
- Exhaust Emissions
Managers must be aware of the accumulation of harmful gases emitted by forklifts. These emissions may contain carbon monoxide, nitrogen oxides, and particulate matter. Installing air extraction and purification systems, complemented with efficient ducting supplies, is essential to address this issue. Ducting systems guide contaminated air out of the facility, reducing the presence of dangerous pollutants. Moreover, these systems minimise the risk of explosions in warehouses where flammable materials are stored.
What to do in Case of Accidents?
Following an accident, the first thing to do is seek medical help. Even if the injury seems minor, it’s important to have it assessed by a professional.
Inform your supervisor or designated health and safety officer as soon as possible. Ask your team to turn off the machines and immediately isolate the area.
Make a detailed record of the accident, including what happened, how it happened, the time and place. Photos or videos can be helpful. If there were witnesses, their accounts should be recorded.
Depending on the accident’s severity, it may be advisable to seek legal counsel or talk to your union representative, especially if there are concerns about safety standards or compensation.
Give yourself time to recover physically and mentally. Some injuries might require a period of rest or reduced duties.
In the event of fatal work accidents, the aftermath can be incredibly challenging. Dealing with the death of a loved one is a profound difficulty, made even more distressing when coupled with financial uncertainty. In such tragic circumstances, it’s important to remember that you might be entitled to compensation. Accessing this monetary support is crucial, as it can help the family reorganise and manage the consequences of such a tragic loss.
Safety in the Warehouse: A Profound Responsibility
In logistics, where every shelf and forklift carries the weight of both economic vitality and potential hazard, the pursuit of safety is paramount. Here, among aisles of ambition, the true measure of success is not merely in the goods dispatched, but in the assurance that every worker returns home unharmed. Ultimately, the greatest inventory a warehouse can maintain is the trust of its people.
Comments are closed.