In the ever-evolving world of warehousing, it’s sometimes easy to forget the basics. Matthew Grierson looks at why safety must always take centre-stage when addressing your racking.
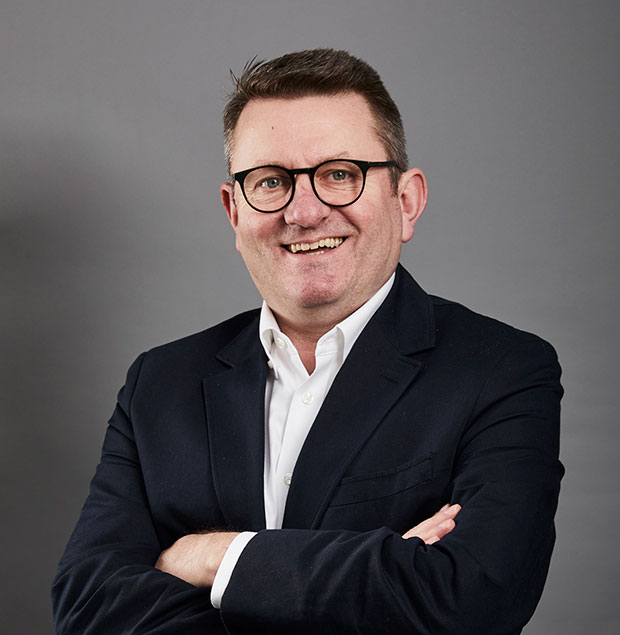
President at SEMA
Warehouse owners often assume that the importance of racking safety only applies at the point of purchase – a job left to your supplier. Yet in our experience, adopting key safety factors at all stages over the lifespan of your racking will make a big difference to workplace safety.
Design and supply
Safety starts with the design of your racking. As the client, CDM 2015 regulations require you to check your supplier’s credentials. Yet, in a market flooded with racking companies, identifying trusted providers can be challenging. Are they working to SEMA Design Codes or European Code EN:15512? Does the structure uphold safety standards for your stock type and throughout the picking process? Ask your supplier if they, like our SEMA Distributor Companies, can prove their credentials and demonstrate, through independent assessments, that their work meets the highest industry standards.
Installation
Next is installation safety. Do not overlook this area, especially when you consider that H&S requirements stipulate that warehouse owners must check the credentials of their installer. It is not enough to simply trust the crew provided by your supplier. If you need to check their ability, ask if they are SEIRS trained. This training programme established by SEMA provides clear guidance that any installer who has passed the SEIRS Diploma has been assessed to the highest industry standards.
Training
Once up, racking can only function correctly if it remains structurally sound. Although designed to accommodate daily wear and tear, any small damage if left unchecked can develop into a serious problem that renders it unsafe. Training, like our Rack Safety Awareness Course, becomes pivotal in maintaining a safe environment. This training instructs employees on identifying racking damage and also explains how to use the equipment safely.
Inspection
Finally, the inspection process which requires a three-tier approach. Every day your staff should monitor and report on racking damage. Then, every week, a trained employee should inspect the racking to check correct usage and loading and document damage levels. The final part is the expert inspection. This is conducted by a professionally qualified racking inspector, such as our SEMA Approved Racking Inspectors (SARI). They provide a detailed report that covers the suitability and compatibility of your equipment, repairs required and recommended timescales.
SEMA
01543 278489
Comments are closed.