In the fast-paced world of food and beverage logistics, it is easy to get caught up in the day-to-day and lose sight of the impact on the end-customer. Today, we interview Shane Faulkner, Head of Sales UK at Swisslog to delve into the transformative power of warehouse automation solutions in the food and beverage industry and explore how these technologies shape the end-customer experience.
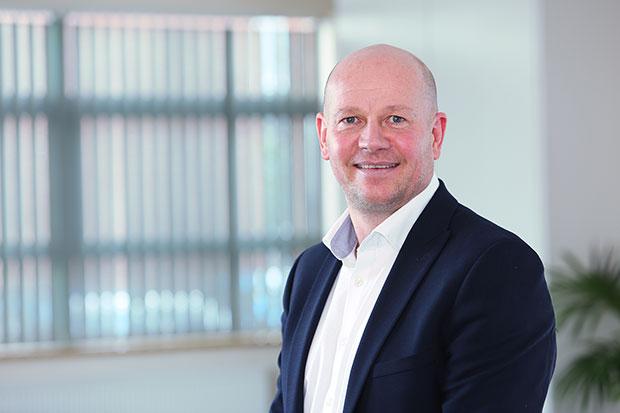
Head of Sales UK
Join us as we uncover the solutions behind the success, sparking new perspectives on the future of food logistics.
How do your warehouse automation solutions contribute to a seamless and efficient grocery shopping experience for customers?
The food industry is changing rapidly due to factors such as new innovations, convenience, healthy alternatives, and dietary restrictions. Consumers are also increasingly interested in being able to track their food all the way from ‘farm to fork’. To stay ahead of the curve, businesses in the food and beverage industry need a flexible operation that can accommodate increased output and shorter turnaround times.
Swisslog’s automated warehouse solutions for temperature-controlled and ambient warehouses provide the agility needed from food production to grocery retail. All our installations are designed around the unique requirements of each operation, ensuring freshness and quality, while reducing costs and order fulfilment time for the end-customer.
What specific benefits do your solutions offer to food and beverage customers, and how do they enhance their satisfaction and convenience?
The challenges of running a warehouse are magnified in the temperature-controlled environment, where standard distribution equipment can’t cope with conditions. Swisslog’s pallet solutions such as PowerStore and Vectura, however, can operate in a wide range of environments, from -30°C in frozen food storage to 50°C in ambient warehouses.
For frozen food warehouses, we have systems that automate manual storage, distribution and order picking processes, improving speed and accuracy. This also keeps operators out of the deep-freeze environment, which ultimately boosts retention and reduces the delays associated with staff shortages.
Can you provide examples of food and beverage companies who have made significant improvements in their customer experience through your automation solutions?
For REWE, a retailer in Germany, we installed our Vectura stacker crane and ProMove conveyor at a new logistics centre, which saves them around one million transport kilometres per year and reduces energy consumption by about 30 percent.
In the UK, leading grocery chain ASDA selected AutoStore empowered by Swisslog. Asda automated its integrated distribution centre to pick at twice the rate with 99.8% accuracy.
Last but not least, Coca-Cola Amatil in New Zealand relies on fully automated processes thanks to Swisslog. The high-bay pallet storage system, CycloneCarrier shuttle system, and ACPaQ palletisation solution all interact seamlessly, delivering efficiency, cost savings, quality, and flexibility.
How do your solutions help in reducing order fulfilment time and ensuring timely delivery of groceries to customers?
It’s no secret that automated picking processes are faster and more precise than manual picking, and Swisslog’s robotic and data-driven logistics solutions optimise the entire storage and retrieval process. AutoStore, for example, consists of robots navigating the storage grid, accurately locating and retrieving the required products.
Additionally, our ACPaQ mixed case palletising solution allows businesses to customise the palletising order to increase efficiency during in-store replenishment. This means groceries get onto shelves quicker, increasing availability for in-store shoppers.
Agile and future-oriented software is also critical for companies to reduce order fulfilment time and keep their warehouse operations optimised at all times. Swisslog’s software management system, SynQ, embeds intelligence in the operation and synchronises the performance of automated logistics systems in the digital era.
All this adds up to keeping order fulfilment times to an absolute minimum and therefore keeping end-customers happy.
What is the scalability of your warehouse automation solutions in the food and beverage industry, and how can they support the growing demands and expectations of customers?
Many Swisslog customers have returned for a second or third installation, or an expansion to their existing system. The mindset is often that automation means rigid technology that quickly outdates, but that is no longer the case. At Swisslog, we are passionate about flexibility and modularity of our systems, so that our solutions support with both existing and future challenges.
Our ACPaQ mixed case palletiser is a highly flexible solution, with semi-automated modules available to suit different requirements. Further automation can then easily be added at a later stage, so that the solution can grow and become fully automated in line with a business’ growth. Equally, the modular design of the PowerStore system opens up completely new possibilities for automation in existing warehouses.
From adapting to evolving consumer demands, to reducing order fulfilment time, these agile and customised installations redefine industry standards. Discover how Swisslog’s innovative technology for the food & beverage industry revolutionises the customer experience, seamlessly integrating convenience and efficiency at www.swisslog.com.
Swisslog
Comments are closed.