Logistex offers automated materials handling solutions and software for warehouses. Specialising in storage, retrieval, robotics, picking, and sortation systems, we integrate industry products seamlessly. Our services include design, implementation, and maintenance of warehouse/ materials handling, along with control systems and software. With facilities management, 24/7 hotline support, and spares, we provide comprehensive solutions for efficient operations.
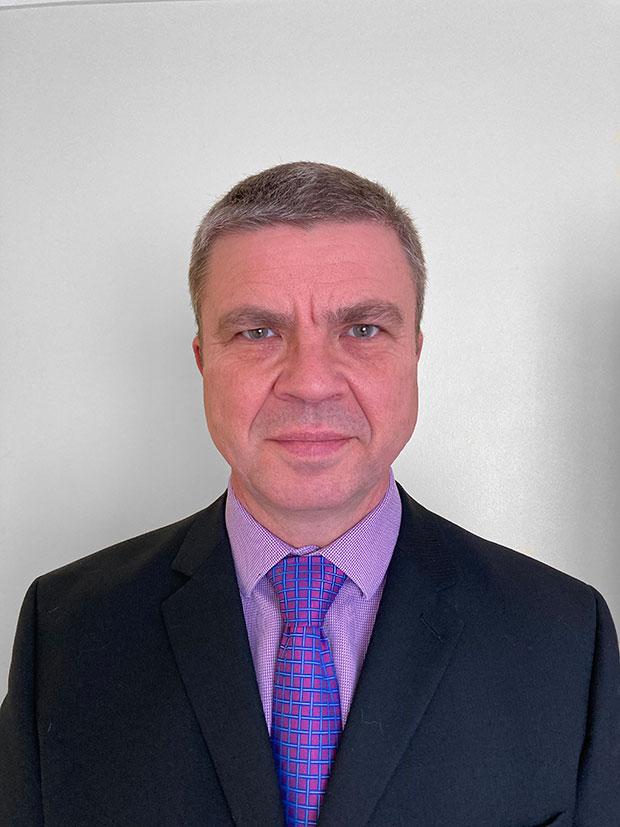
Managing Director
Tony Gruber, Managing Director at Logistex, speaks to Warehouse & Logistics News.
What does your role involve on a day-to-day basis?
I dedicate my time to engaging with customers, suppliers, and colleagues through meetings and conversations. Working in the office allows for casual conversations and learning opportunities, while regular visits to customers’ sites maintains connections and prevents isolation, ensuring alignment and a shared perspective.
What solutions does LOGISTEX offer customers?
Logistex provides comprehensive warehouse automation solutions, handling the entire project lifecycle. We simulate and validate the concept before detailed engineering design begins. Our software team creates custom software and tests it with an emulation model, minimising issues during hardware integration. We integrate hardware and software, conducting rigorous testing, concluding with a site acceptance test. After successful implementation, our Engineering Support Services (ESS) team offers on-site and hotline support for continued operations.
What sectors do these clients work in?
We offer diverse solutions for various sectors including robust pallet-based bulk storage solutions for industries like beverage, food, and paper, order forwarding systems for retailers in fashion, DIY, FMCG, and stationery sectors with eCommerce and store replenishment solutions. Furthermore, we have developed two unique automated systems that directly deliver NHS prescription medicines to patients’ homes.
What are your best products / solutions / services?
Logistex specialises in the Reflex Warehouse Execution System (WES), offering end-to-end solutions utilising advanced automated materials handling equipment. Our Engineering Support Services provide round-the-clock support with dedicated hotlines staffed by UK based engineers. We offer residential site support or a field service mobile engineering service for maintenance needs.
Do you have direct contact with customers, and get involved developing solutions?
Maintaining close customer contact is important to gain a deep understanding of their needs and provide effective assistance. Building strong, long-term relationships with customers is integral to our business approach.
Tell us how LOGISTEX is growing in the UK.
We secure profit by successfully delivering integrated warehouse automation projects within cost, time, and quality budgets. Following the project’s completion, we activate a Hotline support contract for the Reflex WES and a residential site support contract to maintain the automation. These support contracts generate recurring revenue over the site’s lifespan, enabling organic business growth. We prioritise long-term relationships with customers, exemplified by our 30-year support of our oldest customer’s site.
What makes LOGISTEX unique in your industry?
We are an independent logistics automation integrator, allowing us to choose the best automated material handling equipment from various manufacturers to integrate with our Reflex Warehouse Execution System (WES) for a comprehensive solution. As an Employee Owned Trust, every colleague, from directors to field service engineers, is an owner of the business and shares in the profits. This ownership mindset sets us apart and makes a difference in our approach.
How can your solutions help?
The labour market challenges caused by Brexit and the pandemic have increased wages to attract workers, making logistics businesses struggle to recruit enough staff. Our automated picking, packing, order fulfilment, and inventory management solutions reduce the need for a large workforce. Moreover, the roles available in automated operations are more appealing than manual ones, eliminating tasks like extensive walking. Eventually robots will replace human pickers, but the technology is not yet mature enough to handle the diverse range of SKUs in typical customers’ inventories.
What sectors benefit the most from Robotic Solutions?
The most obvious answer is eCommerce fulfilment solutions, but actually there has been an explosion of innovation in robotics and AI in logistics which creates opportunities across all sectors. We are currently developing a robotic solution that provides a cross docking operation for a supermarket’s pallet based dairy products as well as a “traditional” tote based eCommerce fulfilment solution for a leading retailer that utilises multiple robotic technologies. In reality the majority of sectors can benefit from the flexibility, scalability and agility offered by robotic solutions.
What do you see as the biggest opportunities in the coming year for LOGISTEX?
Robotic technology is maturing and becoming more mainstream. Robotic technology allows us to offer more flexible solutions that can be deployed more quickly than traditional automated materials handling equipment as it requires less fixed infrastructure. Our proven track record of successfully designing and delivering highly complex warehouse automation solutions, offering significant returns on investment should create opportunities for Logistex.
What are the biggest challenges facing LOGISTEX and your industry?
Supply chain automation is such a dynamic environment that we have to be able to constantly demonstrate agility, providing solutions that are flexible, scalable and able to cope with changing requirements. Robotics helps to facilitate this.
How future proof and flexible are your solutions?
We plan for 5 to 10 years based on customer forecasts, but accurate design throughput relies on quality forecast data. To accommodate uncertainties, we collaborate with customers to incorporate contingency measures. For example, we recently designed a layout for a customer expecting significant growth and implemented a fraction of the total throughput capacity in the first phase, allowing for 300% growth potential. As anticipated growth materialised, we completed the second phase, resulting in a 100% increase in capacity. Flexibility and scalability are crucial in our solutions, providing options for customers as their needs change. Tell us about a recent project LOGISTEX were involved with.
We successfully completed the second phase of a project for a major online prescription medicine supplier, demonstrating our expertise. The project involved integrating diverse automated materials handling equipment, such as a Schaefer A Frame, CASI Intelligent Prescription Processing machines, Savoye X-PTS tote shuttle system, Savoye carton erectors and closers, and a PC Data Pick By Light system. These components are connected logically via Reflex and physically by Conveyor Units tote conveyor. By integrating equipment from various countries, we delivered a tailored integrated automated solution to meet the customer’s present and future growth needs.
Do you cover the whole of the UK?
Yes. Our ESS team are organised on a regional basis – North, Midlands and South, reaching across the whole of the UK.
What topics are you seeing trending in the industry?
•WES
•Robotics
•Growing awareness of cyber security.
Logistex
Comments are closed.