The Interroll Group is the leading global provider of material handling solutions. The company was founded in 1959 and has been listed on the SIX Swiss Exchange since 1997. Interroll provides system integrators and OEMs with a wide range of platform-based products and services in these categories: Rollers (conveyor rollers), Drives (motors and drives for conveyor systems), Conveyors & Sorters as well as Pallet Handling Solutions. Interroll solutions are in operation in courier, express and postal services, e-commerce, airports, the food and beverage industry, fashion, automotive sectors, and many other manufacturing industries. Among the company’s end users are leading brands such as Amazon, Bosch, Coca-Cola, DHL, Nestlé, Procter & Gamble, Siemens, Walmart and Zalando. Headquartered in Switzerland, Interroll has a global network of 34 companies with turnover of around CHF 559.7 million and over 2,400 employees.
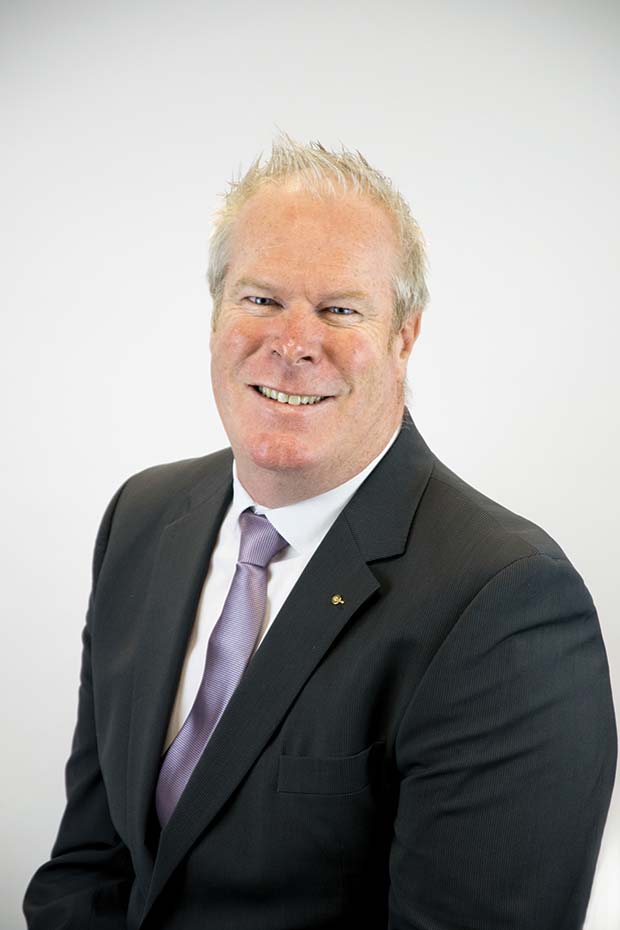
Managing Director at Interroll Ltd
Hilton Campbell, Managing Director of Interroll Ltd spoke to Warehouse & Logistics News.
What products or services does your company offer?
Conveyor Systems
Interroll prides itself on having created ‘platforms’ of products, such as Modular Conveyor Platform (MCP) and Modular Pallet Conveyor Platform (MPP). These ‘platforms’ consist of a wide range of conveyor modules offering enormous versatility. With straight lines, curves, merges and transfers, MCP can offer a wide range of modules consisting of roller conveyors, belt conveyors, lifters, High Performance Diverts and spiral lifts to cover all material flow requirements so that all common materials can be reliably transported.
With MPP, versatile solutions for handling pallets consisting of roller and chain line conveyors, transfers and turntables, comprehensive storage and conveying solutions can be set up for all kinds of applications. Pallets weighing up to 1200 kilograms can be transported at speeds up to 0.5 metres per second.
Pallet Storage
As well as transporting and conveying pallets, the Interroll Pallet Flow system provides a versatile storage system that is based on gravity roller lanes with a decline of 4%. There are no drives to move pallets – instead, gravity takes on this task reducing investment costs, energy consumption and complexity within the installation. Pallet Flow conveyors are available for applications according to the First-In – First-Out (FIFO) and Last-In – First-Out (LIFO) principles.
Sortation Systems
Interroll have two proven solutions for reliable and cost-effective sorting of unit loads such as cartons, parcels, packaged food, etc. These are the Horizontal and the Vertical Crossbelt Sorters, that can be used at various points in intralogistics, such as in the order consolidations and the outbound shipping areas. In response to the increased global demand for fast sorting technology and the growing variety of goods, Interroll launched the new high-performance Crossbelt Sorter MX025H in 2020, which allows higher throughput and can handle loads up to 50 kgs.
Service & Support
Interroll not only has an internal support network for customer support and application queries, but they also have Centres of Excellence that each concentrate on a specific product area and has worldwide responsibility for product management, R&D, production, strategic procurement and logistics as well as providing technical support for local production, assembly and service companies.
Locally we have introduced our own Interroll Lifetime Service team, with our new enhanced offering we can provide a comprehensive suite of services that can be tailored to our customer’ specific needs. For example, predictive maintenance, retrofits for continuous improvements, inspections and repairs.
Do you have any examples of projects you have recently completed?
As a result of the pandemic, it was necessary for operators to create safe working distances for their employees. Interroll was fortunate to be able to secure some significant orders from integrators to create this additional work space. The demand was to supply in high quantities and within short periods, in total we supplied in excess of a quarter of a million pieces to various customers within a very short period. With Interroll’s global capacity and robust supply chain, we were able to continue to deliver on our customers’ needs.
A leading E-Com Company had an ambitious drive to expand in 2020. We secured an order in excess of 2000 pieces of EC5000 Powered Rollers and control cards, rollers and the new Interroll Power Supplies. It was our largest single order to date for this combination of proven technology.
Finally, to share our delivery performance, after booking an order at the beginning of July in excess of 650 metres of zero pressure accumulation, the first delivery step was 6 weeks later, the balance after 8 weeks from receiving the order. Our integrator had the system installed, integrated to WCS level receiving goods by the middle of October. All stakeholders were very impressed on the delivery speed and the speed at which the conveyors could be installed and integrated.
How did the Covid-19 outbreak and subsequent lockdown affect your business?
As with the majority of businesses, the COVID-19-pandemic has had an effect on us all. There have, of course, been projects that have been delayed but we have had no project cancellations. In the first half-year and in specific fields Interroll was able to capture market share, largely due to an excellent delivery performance and innovative solutions.
Did Covid-19 have a negative impact or did the increase in online shopping actually result in a boost to your business?
One of our core markets is Courier, Express, Parcel, including e-commerce. With the accelerated drive to online, Interroll witnessed a significant demand and some orders in these sectors. We do not see this slowing, the fact that many have moved from traditional retailing, to e-tailing, we see continued interest in our products for this exciting sector.
Is your business back to normal following the Covid-19 outbreak?
As far as operations are concerned, Interroll have a fantastic infrastructure of IT and systems to enable business continuity. These were already in place prior to COVID-19, so the impact for workers to function remotely throughout the outbreak was negligible.
There are of course areas of the business such as production and assembly where workers cannot operate remotely. As soon as workers were allowed to return to their places of work that couldn’t work remotely, Interroll put into place safeguarding measures in accordance with local government recommendations & guidelines to keep disruption to supply chains to a minimum.
What training do you provide for your staff?
Interroll has its very own education and training facility, the Interroll Academy. It is the virtual and real platform for transforming the Interroll Group into a learning organisation. Continuous investments in modern learning methods, training facilities and equipment underline our strong commitment to education for our employees as well as for our customers and partners. Furthermore, interactive equipment and hands-on exercises ensure efficient learning and a high level of motivation of our learners.
For us, employee education and continuous development of competences is a core asset and a strategic goal. Therefore, we train our people to be “Best in Class” with respect to customer commitment, responsiveness and knowledge.
Will you be exhibiting at any major trade shows over the next year?
In 2021 we have plans to exhibit at IntraLogistex, IMHX and Robotics and Automation all located in the UK, as well as major trade shows globally such as LogiMAT in Germany. We hope to see and interact with as many customers as possible attending these events as we present our latest technological advances as unfortunately exhibiting at these types of events has not been possible this year.
How would you sum up your company in three words?
Innovative, Reliable, Proven.
INTERROLL LTD
01536 312770
Comments are closed.