Hörmann UK, Europe’s leading door manufacturer, specialises in the manufacture, installation and servicing of a complete portfolio of loading technologies. Hörmann UK is a key supplier for high profile developers across the UK including Prologis, Panattoni, GLP and St. Modwen Industrial & Logistics.
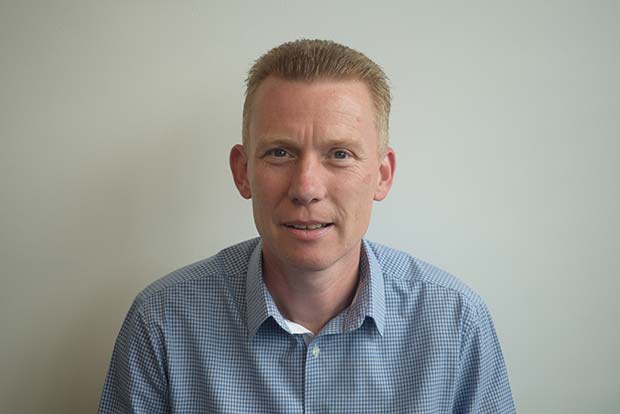
Industrial Division Manager at Hörmann UK
Hörmann UK’s dedication to continuous product development aids developers in ensuring each occupier’s unique requirements are exceeded. From the specification of double deck dock levellers to BBS dock shelters for smaller commercial vehicles, Hörmann’s Project Team applies a bespoke approach to each individual project.
Hörmann UK is also the market leading provider for garage doors and is a leading supplier for entrance and internal doors. Working closely with homeowners, architects, specifiers and housebuilders, Hörmann UK is committed to providing the highest standards in quality, performance and efficiency.
Phil Thorpe, Industrial Division Manager at Hörmann UK spoke to Warehouse & Logistics News.
What products or services do your company offer?
Our high quality products include loading bay systems, level access doors, high speed doors, fire sliding doors and steel door sets.
Which industries do your customers operate in?
The majority of the work we undertake is for major site developers such as GLP, Prologics St. Modwen and Panatonni, whose end users operate in logistics and distribution, increasing for on-line retail business.
Do you have any examples of a project you have recently completed?
We have just completed a major project for GLP at their Magna Park South site, near Lutterworth. The site consists of 4 speculative warehouse units, being 98,000, 126,000, 300,000 and 746,000 sq ft respectively for which we have supplied 150 complete loading bay systems.
How did the Covid-19 outbreak and subsequent lockdown affect your business?
Going into lock-down we furloughed two thirds of our workforce, keeping a skeleton cover in both the Industrial and Domestic sides of our business. The Service Department, however was very much open for business as we recognised the importance of keeping vital food and equipment distribution centres up and running. With all of the Hörmann Group manufacturing plants remaining open during the lockdown there was a steady stream of product being shipped into our Coalville headquarters, a clear commitment to supply from our German colleagues.
Did Covid-19 have a negative impact or did the increase in online shopping actually result in a boost to your business?
As we were able to continue to service and install systems during the lockdown, our industrial business has not really seen a negative impact. As lockdown has eased we have seen a gradual return of confidence in the market and projects that had been pushed back starting to progress. With the growth of online shopping showing no sign of slowing we expect to see continued demand for our loading bays and industrial doors.
Is your business back to normal following the Covid-19 outbreak?
Since the easing of the lockdown we have gradually brought all our staff back to full time employment, albeit we now work a mixture of time split between the office and homeworking. Our sales and service teams are all fully back visiting and assisting customers, whilst taking all the necessary precautions to ensure safe working practices and keeping everyone healthy.
Going forward, will the industry be permanently changed as a result of Covid-19 or will it return to how it was pre-Covid?
The move away from face to face meetings to on-line solutions such as Teams and Zoom will become the norm and the continued growth of on-line shopping and Brexit will see a continued demand for sustainable warehousing in the UK.
What products or services will you be introducing in the next year?
Following on from our launch of Smart control technology in our high speed doors this technology will now be available from 2021 for our sectional and sliding doors.
In what areas are you making technological advances?
As part of our drive to provide a high quality service offering we will be introducing Smart control technology to enable remote access to door information. An online portal will provide information such as error messages and door cycles resulting in shorter service visits and reduced downtime, as wearing parts can be replaced in good time.
What training do you provide for your staff?
The launch of our in-house training academy in 2019 has provided us with a fantastic facility not just to train our engineers but also our trade partners and subcontractors. Innovative ways to continue training during the Covid-19 restrictions are currently being investigated using a mixture of web-based and physical training. This approach has already been adopted by our German colleagues with product training, traditionally undertaken in person, now provided via webinar with up to 40 people from all over the world attending.
What is the company’s commitment to social responsibility?
As a family business, we take our social responsibility very seriously and it affects all aspects of our daily lives. All our plants in Germany are powered by electricity generated from renewable sources. Our UK site in Coalville is powered via solar and all of our products are produced with confirmation of sustainability through our Enviromental Product Declaration.
Our social responsibility also encompasses our people and importantly our customers. Hörmann is proud of the support it affords in our local community, through supporting local schools and sports clubs, but we also get involved in supporting the local activities of our customers and beyond.
What improvements have you made to your customer service recently?
We recognised that an important area we needed to strengthen was our customer contact with site management. This includes overseeing our installations and ensuring the projects are carried out to the highest quality expected of Hörmann UK.
Are you helping customers boost the level of automation in their business?
Our controls are flexible to allow easy integration into automation systems. We also work with our customers and end-users to manufacture bespoke control systems if required.
Do you help customers maximise the use of their existing warehouse space?
Our new range of loading houses are now fully CE marked to EN1090. They are fitted externally, which saves utilising valuable internal warehouse space for the dock levellers. These can be supplied for new build or retrofit.
Will you be investing in your premises over the next 12 months?
We are excited about the continued commitment and investment being made in our UK business and plans have already been agreed to increase stock holding provision, significantly increasing our capacity to speedily modify industrial door panels and generally overhaul and improve the site layout here in Coalville.
What industries do you believe offer your business the most potential over the next year?
While we expect distribution to continue to be busy into next year, we also expect demand to remain firm in other markets such as doors for the Fire and Rescue Service, chilled environments and fire rated sliding doors for distilleries.
How future proof is your business?
With the uncertainties created by both the Covid-19 pandemic and Brexit many parts of the UK building and construction market have come under considerable strain with a shortage of materials and equipment. Through careful planning and access to a multi-national manufacturing Group we are able to show our customers healthy stock levels and lead times. In preparation for Brexit we have invested in additional stock holdings and our customers can be well assured that looking forward our supply chain remains robust and multi-channelled.
How would you sum up your company in three words?
Flexible Innovative Committed.
HÖRMANN UK
01530 516880
Comments are closed.