Throughout 2020 the UK has faced significant challenges and none more so than in the retail industry. Due to lockdown the high street has effectively been closed for a large part of the year and retailers have increasingly turned to online sales.
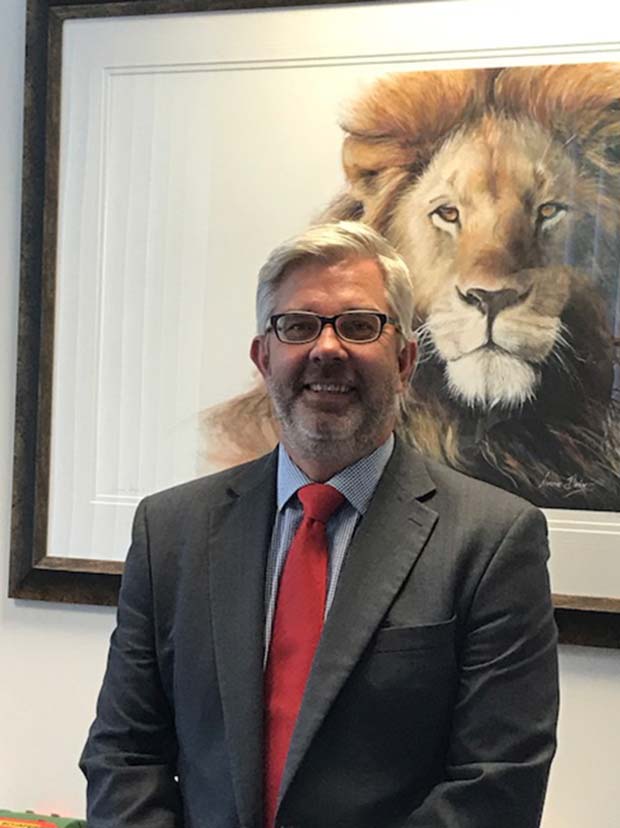
President at SEMA
Statistics show that demand for ecommerce has grown exponentially with online sales in April up by more than 50% compared to last year. This has driven significant demand for new and additional warehousing. There is a bewildering choice out there and safety and efficiency don’t necessarily come at an added price.
Today, safe storage is well within reach when you follow SEMA’s well defined, best practice. As the British Trade Association of the Storage Equipment Industry, our definitive standards have been established gradually but succinctly over half a century. We are committed to promoting the safe design, installation and use of storage equipment manufactured and supplied by our members.
SEMA’s groups are interrelated so to support end users every step of the way. Our guidance has been diligently thought through from project specification, through design, manufacture, distribution and installation involving SAICS and SEIRS personnel. All work to relevant codes and are routinely and independently audited to meet our stringent QA criteria.
Manufacturing
SEMA manufacturers and associates rank among the very best in the world for whom the principles of quality, safety and reliability are fundamental to long standing market success. They are best placed to provide advice on safety risks and other essential requirements. Working closely with statutory authorities, SEMA continues to help each of our groups to continually evolve. Our Technical Committee’s work is respected and continues at both national and European levels.
Demonstrating due diligence, we seek to prove that SEMA products are some of the very best on the market. Members are compelled to continuously engage in independent product design assessments carried out by the University of Salford.
There are never enough hours in the day, but SEMA continues to expand and update a wide range of codes and guides. These are not just for technicians and engineers but are of direct relevance to all those involved with the management and safety of warehouse operations. Together with training these provide a framework for the safe design, installation and use of storage equipment manufactured and supplied by our members.
Supply and Installation
The SEMA Distributor Group (SDG) continues to grow in numbers and strength. Wanting to differentiate themselves from other storage industry operators SEMA Distributor Companies (SDC) follow a three-year cycle of independent audits on compliance standards. This means that every single SDC can prove that their project implementation meets and beats the SEMA QA standard by way of independent certification. Sadly, we know that there are still a number of companies out there passing themselves off as affiliated to SEMA when not entitled to do so. So as the saying goes, “Let the Buyer Beware” and end users should ask to see the SDC’s current audit certificate before signing on the dotted line.
To get the job done right, then choose an audited SEMA Approved Installation Company or SAIC. To become a SAIC member company there is a rigorous application process and a member’s credentials must fulfil exacting criteria. Like SDCs, they are audited and manage installation projects to SEMA’s QA standards.
Installers must be SEIRS registered, the Storage Equipment Installers’ Registration scheme for individual installers. SEMA’s installer training scheme is approved to operate as a Partner Card Scheme of CSCS as it meets the requirements of the Construction Skills Certification Scheme (CSCS). Uniquely, installers are required to take a refresher course every three years.
Rack Inspection & Rigorous Maintenance
Racking collapse and subsequent potential prosecution are simple to avoid where there is a safety culture and correct protocols for inspection, maintenance and repair exist. It’s the duty of an employer to manage risk to life and property and who must always demonstrate a safe system of work.
Staff need to be ‘safety aware’ in that damage is reported immediately, inspections are undertaken weekly or monthly by a suitably qualified individual and the need to employ an external qualified rack inspector to undertake a six monthly or annual audit is recognised.
SEMA Approved Racking Inspectors (SARI) are highly qualified professionals who complete the SEMA circle of quality by undertaking rack inspections at end-users’ premises. They conduct racking and storage condition assessments, reports and recommendations so that all places of employment can operate as safe environments.
SEMA
01543 278489
Comments are closed.