As the second Brexit departure date looms at the end of October an already stretched warehouse property market may have difficulty coping, especially as the leave date will be in the peak Christmas period, exacerbated by the pressures from Black Friday and Manic Monday online promotions.
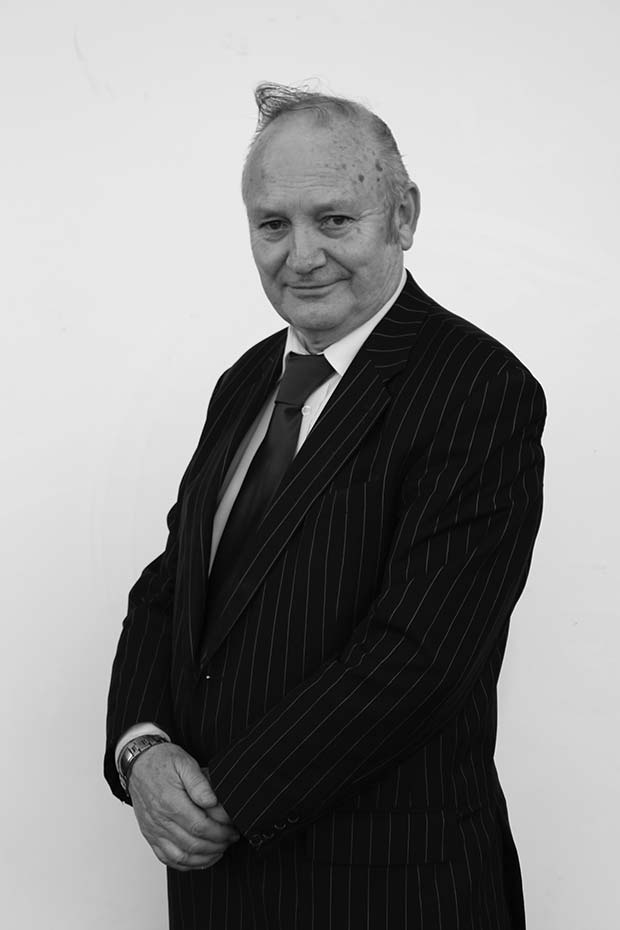
Experts say that there is virtually no additional capacity to cope with stockpiling and Peter Ward, CEO of the United Kingdom Warehousing Association, (UKWA) warns:
“The market as represented by our members is full,” based only, however, on sheds over 100,000ft2. Based on UKWA figures there is, however, a marked vacancy variation in the regional areas, from as little as 2.1% in Eastern England to 10.6% in the West Midlands.
Moreover, the estimated nationwide warehouse vacancy rate of 6.8% in the second quarter of 2019 is slightly up on last year. But are the warnings alarmist and what, if anything, can be done if the market overheats?
Currently about 7.5 million ft2 of new warehousing is under construction but that is only about 1.4% of the 514 million ft2 and “you can’t just turn on supply,” says Peter Ward. Even so, one can locate in areas like the Midlands where not only is the vacancy rate at its highest, geographically speaking, but also the availability of competitive labour is relatively high, a metric that today has greater weight over distance travelled to market. While the Golden Triangle rightly deserves its positons as a prime logistics location, many companies are branching out further. Doncaster is a case in point, where the iPort is located, which is within four hours of 87% of the UK mainland population, but it is also closer to the East Coast deep water ports that service the northern markets, with immediate access to rail lines and motorways. Transport links across the whole of the North will benefit from a £39 billion plan for transport transformation.
Much of the pressure behind what is now a landlord market stems from the rise in e-commerce which requires more warehousing than traditional retailing, and also because new available land in recent years has been used for residential purposes. That pressure, however, could be eased by looking at a flexible space sharing offered by 3PLs. Howard Tenens, a sizeable player in the warehouse market, has some capacity in its portfolio by working in partnership with its network of existing tenants to fill empty space using its infill strategy, says Jamie Hartles, the company’s CEO.
Another pressure reliever could be temporary warehouses, where space permits, ranging from air domes to metal-framed structures, all equipped with the necessary internal controls for keeping stocks in good order. The airdomes are the quickest and cheapest to erect and even the more solid structures can usually be installed within a few weeks from order placement to operation. Available to buy or lease, ‘temporary’ is a misnomer because these structures can give 25 years of service.
Why not also consider using one’s existing storage by adding one or more mezzanine levels? An extension of this long-standing solution is the multi-storey warehousing to fulfil last mile deliveries. It is particularly appreciated where land is scarce and costly and has taken off in America and the Far East in places like Singapore and Hong Kong. These multi-storey warehouses would have HGV ramp access to the upper floors.
Landlords may think that they have the upper hand when negotiating new warehouse lets but that is no reason to lower your guard in such negotiations. A key consideration is to insist on flexibility to move on, so a break clause would be advisable in some circumstances. Avoid landlords who demand both a rent deposit and a personal guarantee. Upward review of rents should be shunned partly in case the landlord has failed to fulfil its obligations over property management.
BILL REDMOND
Features Editor
Comments are closed.