Measuring the order picking rates against labour and fixed costs remains the key yardstick for getting a grip on order picking costs but does the future see robots getting a better grip on costs? Labour can account for 50% of overall warehouse costs, stock-holding costs possibly excepted, and so whenever it is used then time-wasting practices, like excessive walking, must be discouraged, along with the potential for picking errors so prevalent in paper-based picking.
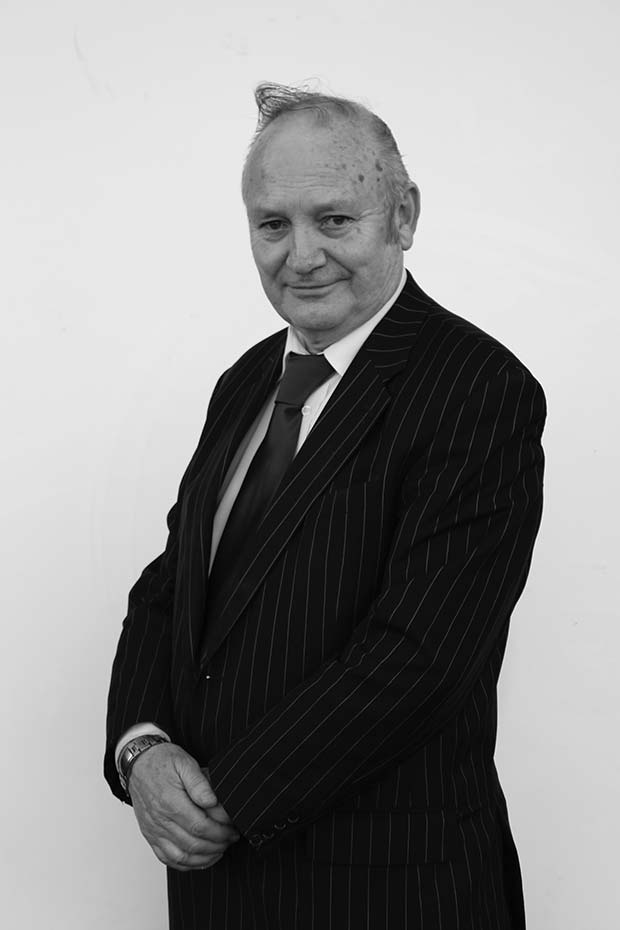
Most distribution centres still use a person-to-goods picking model but the trend among big distribution centres (DCs), especially those offering omnichannel supply services where time-to-customer is critical, is to bring goods to pickers to save on wasted picking time. Typically, these can be mini-stackers, paternosters and carousels, and to see if these are viable investments the DC’s SKU and order activity must be closely monitored and analysed to see how activity levels fluctuate over time. But will it just be a matter to time before the pickers are random robots? There seems no doubt that artificial intelligence (AI) looks set to transform robotic item picking into a reliable and affordable reality. Examples already exist in less complex forms like autonomous AGVs, and now we even have forklifts of various types using geo-guidance systems fitted to standard trucks that make them completely independent of human drivers to self-locate in real time, performing the simplest to most complex jobs even when working around people.
Even so, current order picking robots are limited in what they can pick up, because they can be easily confused by small variations in the size, shape or position of items, whereas the human hand can grasp many different items and work out quickly how to handle objects unseen before. There is, therefore, still a long path to tread until such robot reliability is high enough to avoid bottlenecks, but progress is accelerating as current models advance from repetitive tasks to random tasks, thus making them suitable for complex order fulfilment. Investment costs will also fall.
The degree to which automated order picking will be put will partly be influenced by the nature of the products handled. Where there is little item variety in shapes and sizes the case for optimising the entire material flow and throughput from production to despatch will be strengthened. A good example is Synlait’s infant milk formula site at Dunsandel, New Zealand, which since 2008 has grown to become one of the largest, integrated infant formula sites in the world. Provided by Cimcorp, this multi-pick solution will enable Synlait to transport 1,800 crates from inventory to loading bays every hour. Benefits include significantly increased order fulfilment speed and shorter lead times, resulting in maximising product shelf life – important in any dairy business.
If order picking can be fully automated why not consider at least moving in that direction for the packaging function? This is an area where considerable transport, environmental and packaging materials costs can be saved by right-sizing the cardboard boxes for the packed products. Neopost offers an auto, fit-to-size boxing machine that tailor makes 450 boxes/hr for multiple or single items, particularly useful for ecommerce fulfilment.
BILL REDMOND
Features Editor
Comments are closed.