It’s an age-old question in materials handling: how do operations increase productivity while driving down costs? For many logistics applications, the introduction of robotics offers a worthy return on investment.
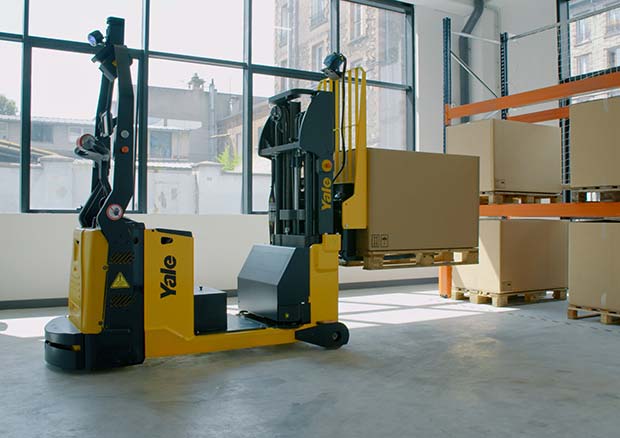
“Industry 4.0 is evolving quickly, and so too is the technology to support it. Yale robotic materials handling equipment can operate without any added infrastructure and is unrestricted by fixed routes, offering great strides forward in terms of flexibility, ease of use and productivity”, said Ron Farr, Warehouse Solutions Manager for Yale.
As the competitive landscape continues to intensify, businesses cannot afford an investment that does not pay off, so translating these benefits from theoretical to tangible reality is key.
Increased uptime and productivity
Supply chain operations are under increasing pressure to get more done in less time with fewer resources. SKU proliferation and the desire for faster delivery times have defined a new “normal”, with services that were once considered perks, such as free two-day shipping, now an expectation for every order.
This demand has triggered a radical shift in logistics applications, with shorter delivery times becoming a driving factor for warehouse overhaul. In this environment, businesses have zero tolerance for downtime, and even minor interruptions can have a severe financial impact.
“Automation is a reliable solution to minimise the risk of downtime and unexpected delays. A robotic truck works relentlessly 24/7, only stopping for battery charging.
Robotic trucks can be fitted with Lithium Titanate Oxide batteries, which can be opportunity charged very quickly and one charger can serve up to five trucks.
“Yale robotic solutions follow speed limits and respond to unexpected obstructions quickly and easily, reducing the potential for downtime resulting from impacts or interruptions and ultimately improving equipment longevity,” adds Ron.
Efficient route planning and adjustment
Automated materials handling equipment in warehouses has historically been bespoke, complex and expensive to purchase and install, resulting in an inflexible solution that is unable to adapt. Industryleading Balyo geoguidance navigation technology is at the heart of the Yale solution, setting Yale robotic trucks apart from traditional automated guided vehicles on offer. With no dedicated infrastructure required, the trucks can operate autonomously without the need for any wires, magnets or reflectors. The Yale solution is fully connected to the customer environment and can be integrated into current processes quickly and easily.
“After consulting with our clients, we recognised a major hurdle to introducing robotics is the installation of dedicated infrastructure. Deploying Yale robotic solutions starts with walking the truck through the warehouse to build a map and learn the main routes, locate storage aisles and other characteristics. Yale robotic trucks, driven by Balyo geoguidance technology, use these existing structural features, such as walls or racks, to build a map of the facility, enabling them to selflocate and navigate in realtime without the need for any physical infrastructure.
“This innovative technology allows the equipment to find the most efficient routes, and adapt to changing inventories and workflows while virtually eliminating the ongoing structural maintenance associated with wires, reflectors and magnets. Even if the facility layout changes slightly and some of the reference points are moved or removed, the robotic equipment can continue to navigate using the remaining features, which gives operations a lot more flexibility,” explains Ron.
YALE
Comments are closed.