SEMA delivers training on Rack Safety Awareness and Managing Rack Maintenance.
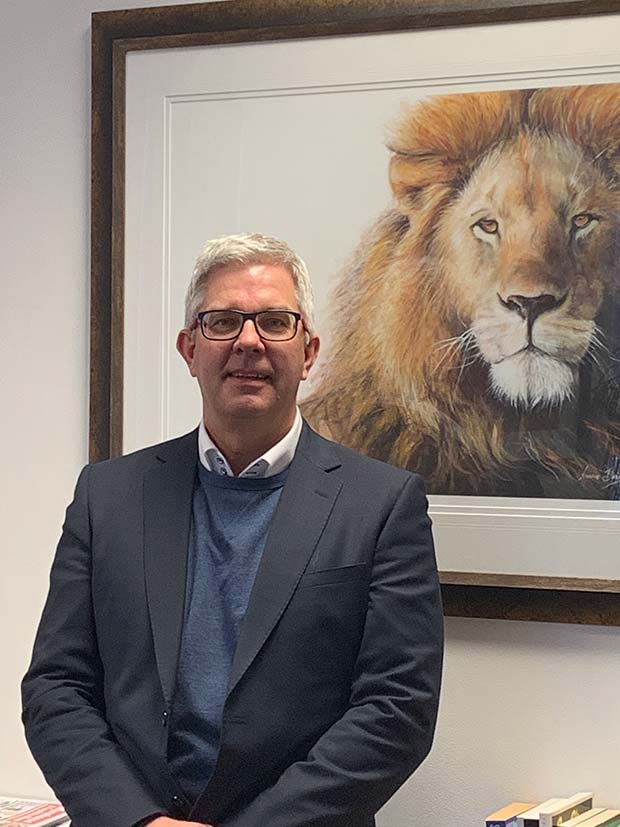
Rack Safety Awareness
Calling managers (including warehouse), supervisors, operatives, team leaders and safety representatives in end-user businesses plus potential inspectors, storage distributors and suppliers; and safety professionals!
You know that storage racking should be properly maintained and in good order. Rack safety inspections are required to prevent and minimise the effects of accidents, to comply with the requirements of PUWER 1998 and to promote safety in the workplace. To help you comply with the most up to date Health & Safety Legislation, SEMA regularly delivers specifically designed key courses.
Rack Safety Awareness is a one-day course providing delegates with advice and guidance to enable them to carry out basic rack inspections in accordance with SEMA guidelines. Two key questions answered are: How often should my racking be inspected? and What are my responsibilities? It also offers advice on conducting risk assessments and how to comply with the law. It also covers types and frequency of inspections, responsibilities of users and suppliers, legislation, recording an inspection, damage levels and action points. A one-day Cantilever Rack Safety Awareness course is also available.
Managing Rack Maintenance
The SEMA Rack Maintenance course is aimed at warehouse managers and supervisors, rack maintenance operations, safety representatives, sales and distribution suppliers and safety professionals. The one-day course consists of an illustrated step by step guide with generic method statements to the safe replacement of damaged racking components. This includes the key differences between maintenance versus repair, identification of key components, how to replace components safely, the replacement of uprights, cross beams and frame bracings. Explaining what is allowable and what is not permitted, the course also identifies the skills needed by professional maintenance teams who need to carry out the replacement of components internally.
A hazard analysis element includes to look out for, handling common hazards, relevant limitations, the use of ancillary equipment and the need for site-specific risk assessments. Delegates also learn about individual responsibilities for managers or supervisors, the maintenance team, the duties of the racking supplier and receive advice on how to liaise with inspectors. Other course content includes relevant codes of practice, the implications of industry-specific regulations and guidance on the interface between officials such as inspectors and maintenance personnel.
SEMA
Tel: 0121 6016359
Email: enquiry@sema.org.uk
Comments are closed.