Hopefully, you have designed your cold store warehouse right first time and are making use of the storage media like racking and forklifts in the most efficient way. What, however, are the warning signs to look for to see if you have come up short in the design process and storage techniques and what are the remedies available?
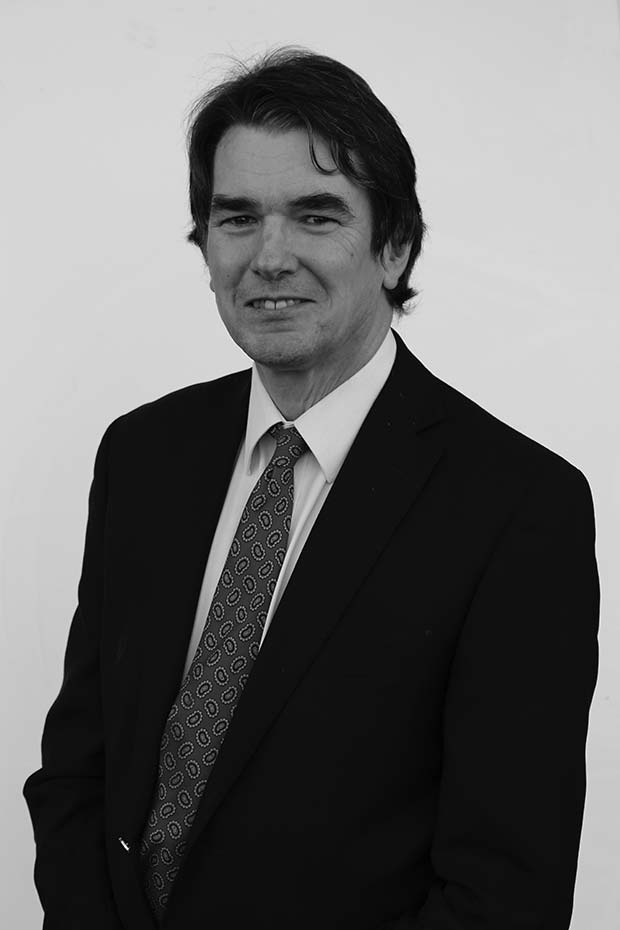
To begin with, the size of the warehouse should be right for you because they are far more costly to build than ambient stores, with energy alone reaching 25% of total running costs. This is where the right choice of racking to give you the stock accessibility rate you desire is so important.
Commonly favoured in cold stores is mobile racking that offers the densest form of storage. Accessibility to stock is high but access times low because time is spent waiting for aisles to be opened and closed so this would not be helpful if one has a fleet of forklifts trying to access loads at the same time. A compromise is the drive-in racking but poor stock rotation, less than 100% instant stock accessibility and notoriously higher accident rates are the downside. A variation of this is push-back storage but lane depth is usually limited to just five pallet loads. Adjustable pallet racking is the least space efficient but does allow 100% instant stock accessibility and good stock rotation, a key factor in a busy store. While wasteful of valuable space, APR, nevertheless, does not have to mean wide aisles if the appropriate forklifts are used. Reach trucks are commonly favoured in cold stores but they need at least 2.6 mt-wide aisles whereas the articulating forklifts fitted with heated cabs, like the Bendi, Flexi and Aisle Master can fit in 1.8 mt-wide aisles.
After the racking issues have been decided the next storage medium is choice of handling kit. Automated stores would use driverless stacker cranes and conveyors but manual stores rely heavily on the choice of forklifts. Having workers inside stores means more attention must be paid to driver health, comfort and efficiency issues and so heated forklift cabs should be considered, which would avoid the need for 15-minute recommended driver breakes.
The intense cold can seriously impact truck performance so careful attention must be paid to batteries, which if not specified correctly can rundown quickly. Fortunately, truck makers are constantly improving their cold store trucks to cope with the hostile environment. A good example is Jungheinrich’s latest cold store High Rack stacker that has an enlarged 86.8 kW battery capacity allowing it to be used for two shifts under normal operations with a single battery charge. Its load lift capacity is also boosted by 100 kg to 1,300 kg. Lithium-ion batteries which tolerate cold temperatures much better than lead-acid are worth considering.
The rise in legislation means that monitoring of temperature and humidity is essential to ensuring safe storage in both warehouses and in transit so it is crucial to keep accurate and consistent records to provide due diligence in upholding these standards. Early detection of threatening temperature and humidity levels like the systems from FilesThruTheAir whose wificonnected data loggers record and stores data to the EasyLog Cloud platform, may not instantly pinpoint the problems but easy, quick detection can prevent significant losses if acted on promptly.
Problem signs include product freezing and shrivelling, discolouration on walls and ceilings, mould and rot. These can be prevented if there is a robust, regular inspection and maintenance schedule. This should include keeping the condenser clean to allow maximum air flow and regular checking of the evaporator coils where there should be no restrictions to the flow of air. If changes in temperature are persistent, there may be issues with the cooling system. The sealing of entrances should be carefully checked for leakage at doors. Good maintenance over temperature issues could prevent multi-million pound losses through product spoilage.
CHARLES SMITH
Feature Writer
Comments are closed.